Work Order Authorization
Authorizing work on a Repair Order in the Service Department
Introduction
The work order authorization process involves reviewing and approving the scope of work, parts, and labor before technicians begin repairs. This ensures the repair aligns with customer needs, confirms inventory availability, and allows proper scheduling.
Authorization also helps track time, labor, and materials for accurate billing and efficient department workflow. Without it, there may be miscommunication or financial discrepancies.
Best Practices:
- Conducting a comprehensive Multi-Point inspection on every customer vehicle ensures that any necessary additional repairs are documented.
- Maintain open communication with the customer and obtain their signature for any extra work added to the repair order.
-
Following the steps outlined below ensures a seamless process for everyone involved.
Initial Work Authorization
When a customer brings their vehicle in for service, the advisor must obtain a signature on the work order for the approved work through the Authorization button.
Once signed, the system will display a checkmark next to the authorized operation.
The "Authorization" button will change to "Authorized" and will be outlined in green, indicating approval.
Additional Work
After the technician completes the multi-point inspection, they notify the service advisor of any recommendations.The advisor then contacts the customer to discuss the recommendations and get approval for any additional work.
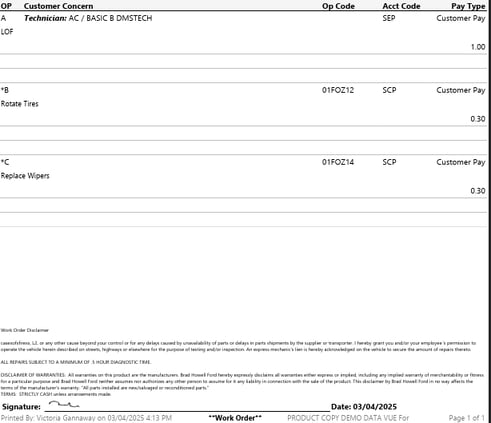
Adding and Authorizing New Operations
If the customer approves the additional work, the advisor adds the new operations to the repair order.The newly added operations will not have a checkmark, and the "Authorized" button will revert to "Authorization."
Important:
The advisor must obtain a new signature from the customer to authorize the additional work.
Finalizing the Authorization
Once the new signature is obtained, the system will mark the new operations as authorized.
The updated, authorized work order can then be printed.
Note:
Following to these steps guarantees that all work carried out is duly authorized, recorded, and accurately processed within the system